煤矿智能仓储系统研究与设计
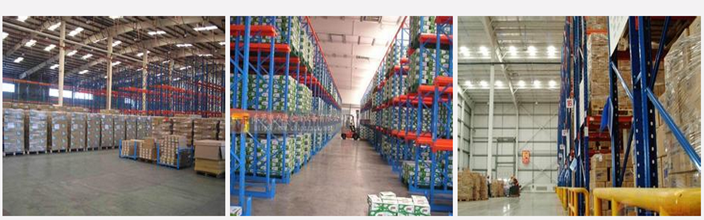
- 仓储粮害虫防治研究进展 [2022-03-03]
- 面向电网企业的仓储配送网络优化... [2022-03-03]
- 基于ISM和BN的危险品仓储系统安... [2022-03-03]
- 转型途中,江苏仓储业期待“轻装... [2022-02-23]
某型无人机通用地面站总装车间智能仓储设计
军用无人机系统在军事侦察、防空预警、战术执行等多个方面都具有重要作用,而无人机通用地面站负责无人机的起飞降落和任务执行等全流程规划,是军用无人机的地面控制核心[1]。某型通地站总装车间通过对产品装配过程的工装管理系统、辅助装配系统、测试系统以及车间仓储物流系统、车间监控平台等多个方面的智能化升级,实现了生产效率和车间管理水平的提升。其中,在车间仓储上合理规划,引入智能仓储管理系统,显著提升了仓储的智能化程度和运转效率;引入自动化立体仓库,显著提高了仓库存储量和空间利用率。
随着机械化、信息化水平以及管理模式的不断提升,智能仓储近年来得到了长足的发展,仓储硬件结构也日趋柔性化、密集化、成熟化和高效化。仓储管理系统作为现代物流的重要组成部分,也已经由过去单一的库存管理,演化为在货物流通中对货品进行全程监测、有效追溯、合理拣选,以及解决供需矛盾的一种重要管理手段。智能仓储正在通过技术手段将以往的“人到货”模式逐步转变为“货到人”模式,不断地提升仓储的运行效率和管理质量[2]。
传统的无人机通地站总装车间在物料存储、记录、送检、送装等过程中主要采用人工方式进行。本文提出一种针对某型无人机通地站总装车间的智能仓储架构设计方法,分别从仓储工艺流程和立体仓库结构两个方面进行阐述,通过关键参数的仿真分析验证设计方法的有效性。
1 智能仓储工艺流程规划
合理的工艺流程规划能够充分挖掘先进技术在智能仓储中的应用潜力。工艺流程的规划依赖于生产现场具备的设备资源与工艺资源,因此智能仓储的功能模块架构和管理系统的层级分析是必要的。
1.1 智能仓储功能模块架构
该车间智能仓储主要由立体仓库结构件、输送部件和管理系统3个主要模块组成,系统架构如图1所表示。
完善的智能立体仓储系统不仅需要成熟的硬件设施来完成物料的流转,更需要管理系统来协调仓储过程、仓库与车间物流对接过程和仓库与生产制造系统对接过程。物联网、RFID(Radio Frequency Identification)等技术的应用使得立体仓储管理系统趋向简洁化、智能化、高效化[3]。立体仓储的管理系统架构如图2所示,其主要软件系统为WCS(Warehouse Control System)与WMS(Warehouse Management System)。两者作为设备层仓储工控设备的控制系统,同时也是仓储系统与生产制造系统的执行层、计划层的数据交互接口[4]。
1.2 智能仓储工艺流程梳理
传统的仓库多采用到货—测试—检验—入库的串行流程。在该通用地面站总装车间中,通信设备所需的测试时间较长,如果单次到货量较大,则容易在测试区形成物料积压。该车间使用并行流程来替代传统仓库的串行流程,将检测合格与未检测的产品物料共同放置于立体仓库中,通过WMS中记录的与条码对应的检测状态来区分该物料是否检测过以及是否检测合格。
该总装车间整体分为仓储区、检测区、返修区、装配区等区域,物流路线如图3所示。
图3中虚线区域内为智能仓储的功能分区。从物料入所到产品装配上车的整个生产过程中,智能仓储参与以下几个流程:到货入库、送检出库、检完返库、送装出库、送装返库、送修返库等。每个流程的具体工艺步骤和使用的工艺资源如表1所示。
借助条码识别技术,在各个环节中当物料状态发生变化时均进行扫码识别并录入系统,以保证对每个物料状态的实时获取。关于不同状态的物料在立体仓库中的存放需注意以下两点:
(1)检验不合格的物料将不会返回库中而是送修或者返厂,并同时将对应状态录入系统。此举可以保证立体仓库中只存在未检验和检验合格的物料,而不存在已检验但不合格的物料。
(2)检验完返库的物料应避免放入装有未检物料的料箱中,到货入库的未检物料避免与已检验合格的物料放于同一料箱中。此举保证同一料箱中物料检测状态的一致性,降低分拣难度且便于管理。
2 智能仓储结构设计
2.1 仓储结构设计路线
仓储结构设计的依据主要来源于两点:梳理的存储对象物理参数和仓储行业标准。本文提出的智能仓储结构设计路线如图4所示,整体思路为通过梳理物料数据确定需求参数,继而在行业标准的框架下逐步确定从料箱到立体仓库的设计参数。
在上述设计依据的指导下,首先从物料需求出发,分析物料的体积与重量特点,选定需要放入立体仓库的物料。座椅、席位台等物料体积明显大于其他物料尺寸,则单独存放于立体仓库外。对选定存入立体仓库的物料进行高度量纲统一化和重量梳理,继而在标准料箱系列中选取合适的型号。根据仓储的出入库频次要求和成本控制需求等确定仓储的类型,再由料箱的尺寸与立体仓库总体尺寸范围共同确定立体仓库的结构尺寸细节,最后以立体仓库容量作为适应度函数来验证设计结果是否符合产能和库存量等要求。
2.2 仓储关键参数设计
2.2.1 料箱参数选定
料箱的选择以物料的体积为主要推算依据,以同一料箱中的物料总重量为检验依据。料箱尺寸参数的设计路线如图5所示。
该无人机通用地面站物料的物理属性具有长度区间化、高度规格化和宽度统一化的特点,以标准工控机箱为主,异型件为辅,其中,工控机箱高度以U作为单位。针对以上特点,本文提出使用高度量纲统一化的策略作为料箱参数选型方法。
产品物料中机箱高度有1U~5U共计5种规格,截面积也都小于520 mm×650 mm,则在系列中选择面积为600 mm×800 mm的料箱。将非工控机箱的物料按厚度折算成对应的U数(如图6所示)。图中将物料脚蹬等效放置于以U为单位的空间中,则两个并排脚蹬等效空间为5U,单个脚蹬记为3U。
考虑到物料高度最大为5U,大部分物料的厚度(2U~3U)能整除6U,物料堆叠使用隔层等情况,确定单个料箱需要的有效装载厚度为6U。鉴于料箱本身具有弹性内衬和防尘盖,则在尺寸系列中选择高度为345 mm(约7.76U)的料箱,最终料箱规格确定为800mm×600 mm×345 mm。
单个料箱中存储的物料总重量均小于100 kg,该标准料箱符合重量要求。
2.2.2 立体货架结构设计
立体货架设计的整体步骤是:首先确定货架的结构形式与货位分布形式,再根据具体形式货架的设计规则进行参数的确定。本文主要阐述结构形式与货位分布的确定方法。
在诸多货架结构形式中,牛腿式货架(也称贯通式货架)在生产车间中使用较为广泛,其优点也比较鲜明:(1)存储密度高,仓库利用率高;(2)工作效率高,大大减少作业等待时间;(3)作业方式灵活,货物的存取方式多样;(4)安全性好,能够减少货架碰撞,提高安全生产率。鉴于此,智能仓储的立体货架结构选择牛腿式货架。货架的结构由立柱、连接杆、可调底脚、横梁、托盘导向板、牛腿、防撞杆、叉车定位板等组成。
牛腿式货架的货位分布除了普通的双侧单货位布置,还有双深位布置形式,即在巷道两侧各分布两列货位。本车间规划的仓储占地10 m×20 m,相同占地面积可以布置成普通仓储和双深位仓储两种格局。在现有空间限制下,两种方案的货位排布示意图如图7所示。
从图7中看可以看出,在限定的仓储区域中布置立体货架和滚筒传送带后,两种方案的立体货架具有相同的层数(12层)和列数(17列)。两种形式货位分布的区别在于普通立体仓库有6排货架和3个堆垛机,而双深位货架有8排货架和2个堆垛机。普通立体库1224个库位,双深位立体库1632个库位。
考虑到两者货位分布方案占地面积一致,那么通过货位数对比可知:采用双深位立体货架在普通立体货架基础上空间利用率提升了33.3%,在空间利用率上占有优势。
成本方面,堆垛机在立体仓储硬件建设成本中占据的比例最高,普通立体仓库由于堆垛机台数多,其成本高于双深位立体仓库;运转效率方面,双深位立体仓库中一个巷道的堆垛机要负责4列货架的物料存取,且存取外侧货架的货物时可能需要移库,存取效率不及普通立体库。
综合分析两种类型的仓储货位分布,其特点如表2所示。
本车间采用站位式装配,出入库效率均低于50周转箱/小时。对于仓储的出入库频次要求不高的情况,提高仓储空间利用率、降低投入成本是关键决策因素,故双深位立体货架形式更符合设计目标要求。
2.2.3 输送系统设计
输送系统是智能仓储的主要运动部件,起到物料载体的作用。该系统主要包含库内运送部件和库外输送线,库内输送一般由穿梭车或者堆垛机来实现,而库外输送线一般由滚筒输送线和移载机来实现。
对于库内输送部件,穿梭车和堆垛机各有优势,具体如表3所示。
穿梭车一般用于穿梭式货架仓库,而堆垛机用于传统堆垛机仓库。考虑到通用地面站的涉密性,车间内部应当避免使用WIFI等无线通讯方式,同时堆垛机技术成熟稳定,维护成本低,同一巷道取货效率高,因此该总装车间选择堆垛机方案。
由于该总装车间均为小于80kg的轻型物料,对堆垛机承载力要求不高,所以具体型号选取时考虑因素主要为堆垛机运动速度、安装高度以及成本。最终选择的堆垛机关键参数见表4。
对于库外输送部件,一般由输送机与移载机组成。输送机可分为滚筒输送机、皮带输送机、链板输送机等。滚筒输送机适合底部是平面的物品输送,同时具有结构简单、可靠性高、使用维护方便、运转速度快、输送量大、可多品种共线分流等诸多特点,满足该总装车间的料箱传送需求。因此,本车间选定滚筒输送线配合箱式顶升移载机实现物料的库外输送。滚筒输送机的关键参数为额定输送载荷150 kg,输送速度20 m/min。
2.2.4 仓储容量评估
在生产系统中,仓储容量是影响车间产能的重要因素。合适的仓储容量既能避免库存偏大导致的元器件防护成本提高,也能防止库存较小导致的齐套性差与产能不足。由于该总装车间采用站位式装配,个别物料的缺货会直接导致整车装配的停滞,所以物料的齐套性尤为重要。因此,在估算仓储容量时,以能够装载多少套通用地面站方舱的全部零配件为评估标准。
仓储容量取决于立体仓库总库位数和单套产品物料所需库位数。双深位立体仓库共计1632个货位,除去线缆和标准件、紧固件等,预估有1500个货位容纳普通装配物料。
该通用地面站一套产品由两辆车组成,分别为任务站与起降站。每辆车的前舱为操作舱,后舱为机柜舱,具体舱内物料种类与个数如表5所示。
按高度量纲统一化方法可以得出两种车不同U数的机箱数量如图8所示。在物料存入立体仓库时,遵循同一料箱只摆放同一种物料、可摆放多个物料的原则。在计算过程中,大体积机箱具有不可拆分性,单个料箱中4U~5U的物料只能放置1个,所以4U~5U的物料体积在计算仓储容量时统一定为6U。
n套通用地面站需要的货位N的估算表达式如式(1)所示:

式中:i为第i种物料;A为单个任务站的物料种类数;B为单个起降站的物料种类数;ai为每个任务站需要第i种物料的个数;bi为每个起降站需要第i种物料的个数;ni为第i种物料体积对应的U数;n0为料箱中有效容积的U数,这里n0=6;
在计算立体仓库容量时,采用试算法,操作方法为从n=1开始不断增加n的值进行试算,直到N接近1500。则可以得出:n=14时,N=1481;n=15时,N=1570。
因此,该立体仓库至少能存储14套通用地面站的所有方舱内零部件,能够满足该总装车间的产能需求。
3 结束语
为了满足多品种、小批次、高度定制化的无人机通用地面站物料仓储需求,本文提出了相应的智能仓储工艺流程规划方法与具体的结构参数设计路线,具体结论如下:
(1)通过将串行流程优化为并行流程,并对工艺流程进行重新梳理与优化,有效提升了仓储运转效率;
(2)借助物料梳理—料箱选定—仓储形式确定—具体参数计算的总体设计思路,可以有效解决智能仓储货架参数设计问题;
(3)通过高度量纲统一化,可以快速高效地完成物料梳理、料箱尺寸确定以及立体仓库容量评估;
(4)在出入库频次要求不高的情况下,双深位分布结构比普通仓储结构具有更高的空间利用率和更低的建设成本,十分适合于多品种小批量且出入库频次低的物料产品的立体化存储。