煤矿智能仓储系统研究与设计
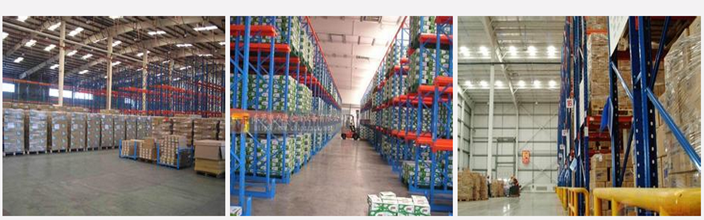
- 仓储粮害虫防治研究进展 [2022-03-03]
- 面向电网企业的仓储配送网络优化... [2022-03-03]
- 基于ISM和BN的危险品仓储系统安... [2022-03-03]
- 转型途中,江苏仓储业期待“轻装... [2022-02-23]
仓储过程中货位指派优化问题研究
自动化立体仓库集仓储、输送、分发于一体, 已广泛应用于包装与物流领域, 特别是货物的仓储过程。在货物仓储过程中, 需要对每件货物进行货位指派, 为每一货物分配恰当的储存位置, 即在恰当的储存方式下的空间储位的分配[1]。货位指派直接影响着自动化立体仓库的仓储效益, 因此, 在仓储管理、自动化立体仓库管理中, 货位指派优化问题是一个关键问题[2,3,4,5,6,7,8]。本文以某烟草公司自动化立体仓库系统为例, 将货位优化问题归结为货位的二次指派优化问题, 采用遗传算法对实例进行优化分析。
1 货位指派优化问题分析
1.1 存在问题分析
该烟草公司的自动化立体仓库是一座以叉车为运输工具的中小型自动化立体仓库[8], 它主要负责所在地区烟草配送, 进货量大、多用户、多品种、小批量发出, 货物周转速度较快, 几乎不存在货物积压的情况。目前, 该仓库在货位优化方面主要存在两个问题:
1) 对货位指派问题没有进行优化分析。每次进货时, 系统首先查找到仓库中的空货位, 并将进货任务平均分配给每辆叉车, 所有叉车同时执行入库任务, 将货物随机放入找到的空货位, 直到最后一辆叉车完成任务为止。进货时, 叉车首先在入货台叉取码放好货物的托盘, 然后再返回到各自的巷道完成入库任务。由于每条巷道口至入货台之间的距离不同, 按进货数量平均分配任务后, 易造成各叉车工作时间差较大、使用频率不均衡甚至过度使用等情况。
2) 忽略了不同品牌香烟存取频率的差异, 统一进行货位指派。由于货物的存取频率对仓库的整体效率影响很大, 故应该将存取频率作为货位指派优化问题中的重点考虑因素。
1.2 二次货位指派优化思路
基于文献[8]中给出的自动化立体仓库的三维模型描述、叉车从入货台到任何货位的运行时间计算方法, 本文提出二次货位指派优化方法, 即进货时首先搜索出一组最适合的货位, 并将这些货位按时间大小排序;然后再将这些货位优化指派给不同存取频率的香烟。
二次货位指派优化目标是使各个叉车工作时间尽可能均衡, 用最少的时间进货, 同时考虑不同品牌香烟的存取频率, 将出入库频率高的货物安排在存取时间小的货位。第一步, 进行第一次货位指派。采用遗传算法对仓库中空货位进行搜索, 选出一组最适合的货位分配方案, 将这些进货任务分配给所有叉车。优化目标是使所有叉车同时工作, 且最长时间 (指一次进货任务中, 最晚完成任务的叉车的工作时间) 最小, 最长时间和最短时间 (指一次进货任务中, 最早完成任务的叉车的工作时间) 差最小。采用这种方法可保证各个叉车工作时间均衡, 且总体进货时间最短。第二步, 在第一次指派的基础上对货位进行二次分配, 即第二次指派货位[9]。考虑到不同品牌香烟的存取频率不同, 存取频繁的香烟应具有较短的存取时间, 将存取频率高的香烟放置在出入库时间短的货位上, 以保证仓库的整体效率最优。在单位时间内, 叉车取放某种香烟的工作量与这种香烟的出入库频率和存放位置有关, 将该香烟的出入库频率乘以叉车运行至存放货位所用时间作为权值因子, 即
Eij=fi×tj (1)
式中:fi—第i种香烟的出入库频率;tj—叉车从入货台到货位j取放货物的标准时间, 且tj=TT, TT—叉车从入货台到达该货位的运行时间[8]。在第二次指派优化问题中, 优化目标是使权值因子总和最小。
1.3 第一次货位指派优化算法
对于第一次货位指派优化问题, 常用的优化算法较多。考虑到该烟草公司的自动化立体仓库进货量大、多用户、多品种、小批量发出, 以及遗传算法操作简便、寻优能力强等特点[8,10], 选用遗传算法分析第一次货位指派优化问题, 优化算法流程图见图1。首先进行初始化, 计算叉车从入货台到各个货位的时间, 并按时间大小将货位排序。然后确定群体规模、繁殖代数、交叉概率和变异概率, 将交叉和变异作用于种群, 以交叉和变异后的结果不能超出巷道中现有空货位数作为约束条件进行修正。进化运算后, 判断是否达到终止条件。若达到, 选择适应度函数值最大者作为第一次货位指派方案, 算法结束;否则返回变量编码, 继续进行优化计算。
2 算例分析
针对某烟草公司的自动化立体仓库[8], 入货台到货架的垂直距离7m, 巷道宽度3m, 货架宽度1.2m, 两货架间距0.5m。叉车在水平方向上匀速运动速度0.25m/s、加速度0.00625m/s2, 垂直方向上匀速运动速度0.2m/s、加速度0.0133m/s2。
对二次货位指派优化算法进行了9组验证分析, 库存率分别为0、10%、20%, 进货量分别为100、200、300组 (每组为24箱烟, 码放在一个托盘上) 。有A、B、C、D、E、F 6种香烟, 存取频率分别为30%、20%、15%、15%、10%、10%。选取最大迭代次数max Generation=1000。当Generation=400时, 算法终止, 优化结果见表1、2。
例如, 当进货数量100组 (2400箱) 、库存率10%时, 优化前完成一次进货任务需6309.3s, 而优化后只需2589.4s, 节约了3719.9s, 总时间缩短了58.9%;权值因子E值 (即出入库频率乘以叉车运行至存放货位所用时间) 由优化前的3865.9s缩短到优化后的2233.2s, 减少了1632.7s (42.2%) ;而最大时间与最小时间差值由优化前的4370.8s缩短到优化后的174.9s, 减少了4195.9s (约96%) 。
显然, 这种货位指派优化方法可显著提高进货效率、仓库整体效率, 优化各叉车使用频率、均衡工作时间, 避免某辆叉车的过度使用。
表1 二次货位指派优化结果 导出到EXCEL
Tab.1 Optimization Results of two times assignment of cargo location
序号 |
1 | 2 | 3 | 4 | 5 | 6 | 7 | 8 | 9 | |
库存率/% |
0 | 10 | 20 | 0 | 10 | 20 | 0 | 10 | 20 | |
货物数量/组 |
100 | 100 | 100 | 200 | 200 | 200 | 300 | 300 | 300 | |
最大时间 /s |
优化前 |
6027.3 | 6309.3 | 6759.3 | 18040.6 | 19600.6 | 20794.6 | 36067.9 | 38387.9 | 41858.9 |
优化后 |
2481.4 | 2589.4 | 2627.5 | 5763.1 | 5896.1 | 6155.2 | 9611.7 | 10304.5 | 10604.3 | |
差值 |
3545.9 | 3719.9 | 4131.8 | 12277.5 | 13704.5 | 14639.4 | 26456.2 | 28083.4 | 31254.6 | |
最小时间 /s |
优化前 |
1887.4 | 1938.5 | 2031.6 | 4505.4 | 4657.5 | 4957.6 | 7785.4 | 8115.5 | 8765.6 |
优化后 |
2383.3 | 2414.5 | 2454.9 | 5235.9 | 5586.4 | 5832.6 | 9356.8 | 9459.3 | 10127.3 | |
E值 /s |
优化前 |
3734.4 | 3865.9 | 4180.4 | 10770.5 | 11440.3 | 12551.8 | 20832.5 | 22025.9 | 23904.0 |
优化后 |
2192.7 | 2233.2 | 2291.5 | 5061.6 | 5190.6 | 5389.7 | 8268.9 | 8547.4 | 8946.9 | |
差值 |
1541.7 | 1632.7 | 1888.9 | 5708.9 | 6249.7 | 7162.1 | 12563.6 | 13478.5 | 14957.1 |
表2 进货时间比较 导出到EXCEL
Tab.2 Comparison of cargo entrance and stock time
序号 |
1 | 2 | 3 | 4 | 5 | 6 | 7 | 8 | 9 | 平均值/% |
优化前后进货时间缩减率/% |
59.0 | 58.9 | 61.1 | 68.1 | 69.9 | 70.4 | 73.3 | 73.2 | 74.7 | 67.6 |
优化前后E值缩小率/% |
41.3 | 42.2 | 45.2 | 53.0 | 54.6 | 57.1 | 60.3 | 61.2 | 62.6 | 53.1 |
最大时间与最小时间差值缩减率/% |
97.6 | 96.0 | 96.4 | 95.9 | 97.9 | 98.0 | 99.1 | 97.2 | 98.6 | 97.4 |
3 结语
针对某烟草公司自动化立体仓库系统, 将货位优化问题归结为货位的二次指派优化问题, 研究优化思路和算法, 并采用遗传算法对实例优化分析。这种货位二次指派优化方法可行有效, 可显著提高进货效率, 优化叉车使用频率、均衡工作时间, 从而保证整个仓库的效率最优。