煤矿智能仓储系统研究与设计
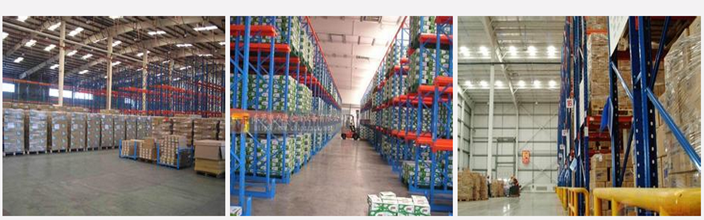
- 仓储粮害虫防治研究进展 [2022-03-03]
- 面向电网企业的仓储配送网络优化... [2022-03-03]
- 基于ISM和BN的危险品仓储系统安... [2022-03-03]
- 转型途中,江苏仓储业期待“轻装... [2022-02-23]
基于Flexsim的物流仓储系统的建模与仿真
1 引言
物流仓储系统是典型的现代机械与电子技术相结合的系统, 由具有一定智能的物流设备和计算机管理与控制系统组成。随着国内企业规模越来越大, 拟建设的物流仓储系统变得越来越复杂, 其内部关联性越来越强。企业在面临物流工程项目投资新建或原有系统技术改造时, 由于缺乏准确丰富的信息数据和必要的物流仿真系统决策支持, 造成项目建设投入的盲目性和资金流失。为了避免在物流仓储系统优化构建上浪费大量的人力、物力和时间, 物流仿真是必然的选择。
本文讨论基于Flexsim开发平台的物流设备仿真建模方法, 分析物流仓储系统仿真模型的组成, 研究仓储系统仿真建模的核心思想和基本思路, 总结归纳资源类设备和执行类设备基于Flexsim开发平台的行为实现、运动实现等仿真建模问题。
2 基于Flexsim的物流仓储系统仿真实现
2.1 系统建模
以总体设计方案及相关设备技术参数作为前提和依据, 先确定仿真系统各个模块的构成和连接关系, 以系统设备设计参数作为仿真参数, 分别构建各相关子系统模块, 然后根据物流作业流程编写控制程序, 连接各子系统模块组成系统模型。
本文研究的某集团仓储系统平面布局如图1所示, 其按作业性质不同可以分成如下功能区域:收货组盘区、集货区、储存分拣区以及发货区等。其中储存分拣区为仓储系统的主生产区, 包括主储存区 (AS/RS 3跨区) 、整箱分拣区、拆零分拣区、补货区等, 其余为辅助生产区。主储存区总容量为22 230个货位, 15个巷道, 每个巷道由2列13层货架构成;整箱分拣区由上下2层1 688个拣选位构成。该仓储系统主要存储托盘物料和整箱物料2种货品。主要设备配置参数见表1。
该仓储系统功能结构如图2所示, 包括功能模块层、设备系统层、物流设备层, 其中收货组盘区、集货区、发货区的规划和设计较简单, 建模也相对较容易。储存分拣区是整个仓储系统仿真设计的重点和难点, 分解为几个设备系统, 包括AS/RS系统、分拣系统、输送系统、搬运系统。自动分类分拣区主要由自动分类系统组成, 设备系统主要由输送机和操作人员组成, 完成物料的拆零分拣工作。本文仅介绍整个仓储系统的AS/RS系统和整托盘拆零分拣系统的建模方法和过程。
表1 仓储系统主要设备配置参数 导出到EXCEL
名称 | 数 量 | 主要性能指标 |
货架区 |
巷道数:15个 货架数:30排 |
货架列数:57 货格载货数:2 货架层数:13 |
整箱分 拣区 |
巷道数:36个 货架数:72排 |
货架列数:28 货格载货数:2 货架层数:2 |
入库区 | 入库口:3个 |
整托盘入库口:2 箱式入库口:1 |
出库区 | 出库口:16个 |
整托盘分拣口:6 拆零分拣口:7 整箱出库口:1 补货口:1 |
堆垛机 | 堆垛机数:15台 |
货叉速度:30 m/min 运行速度:150 m/min 起升速度:40 m/min |
输送机 |
托盘输送机:167台 箱式输送机:1套 |
输送速度:16 m/min |
2.2 AS/RS系统的仿真建模
AS/RS系统仿真模型以货品订单到达和配送车辆将货品送达出库月台为边界, 描述整个物流仓储中心运作的外部条件和内部条件, 模拟仓储物流中心内的各主要操作和管理过程。整个系统仿真包括订单处理、入库、储存、整托盘拆零分拣、出库作业流程。本文拟通过利用系统仿真技术, 全面仿真系统运行情况, 研究系统运行瓶颈环节, 考察物流设备利用率, 最终确定物流量能否满足需求, 对现有资源配置下的最大货品周转量进行分析。
2.2.1 仿真模型的建立
对AS/RS仿真系统做如下假设: (1) 设计时不包括流通加工环节; (2) 对货品出入库策略进行仿真模拟, 运用堆垛机进行货品的补货入库、上架操作; (3) 对货品分拣策略进行仿真模拟, 通过货品在货架区储存时间的长短来表示货品拣取策略, 由操作人员进行货品分拣操作。
仿真平台中已有初始模型的一些物流常用设备可通过参数设置建立模型, 如高层货架设置排、列、层数及货格尺寸等参数, 巷道堆垛机设置X、Y、Z方向的速度及加速度等参数, 并定义行进路径及各台堆垛机小车工作、停车、送货的优先列表等。
AS/RS系统模型建立后, 通过Flexscript编程语言, 根据仓储系统作业流程编制货品流程控制程序, 控制整个系统各种货品的运动流程和货品流量的大小, 以及单机设备的动作关系等。货品的出入库流量根据实际工作状态选用固定常数值或正态、指数等随机分布数值。AS/RS仿真系统出入库作业控制流程如图3所示。
2.2.2 仿真模型参数的设定
假设该仓储系统每天8 h入库作业, 10 h出库作业, 最大入库作业量94盘/h, 最大出库作业量为100盘/h, 平均入库作业量为37盘/h。根据以上设备参数的性能指标, 在Flexsim开发平台对仓储系统抽象和简化, 进行资源类设备和执行类设备的参数设定:
(1) 资源类参数的设定 ①订单生成器、货品生成器 (Source) 参数的设定如表1所示;②货架参数的设计如表2所示;③入库处理器 (Combiner) 参数的设定如表3所示, 最大入库量为94盘/h, 即每38 s有1托盘处于装盘入库触发状态;④分拣处理器 (Separator) 参数的设定如表4所示。
表1 货品生成器参数 导出到EXCEL
FlowItem Class | Pallet | |
Inter-Arrival time | Exponential distribution | exponential (0, 10, 1) |
Oncreation | setitemtype (item, duniform (1, 15, 1) ) | 设置不同类型的托盘入库 |
addlabel (item, “ItemID”) ; addlabel (item, “Item_Separator”) ; addlabel (item, “Item_Num”) ; |
在托盘实体上设置自定义标签变量, 其中“ItemID”值为1时, 表示整托盘出库;为2时, 表示托盘通过操作人员拆零分拣出库。“Item_Separator”值为0时, 表示该托盘未进行分拣;为1时, 表示该托盘已分拣过。“Item_Num”值为0时, 统计该托盘上存放的箱数;当Item_Num<2时, 托盘不能进行拆零分拣, 整托盘出库。 |
表2 货架参数 导出到EXCEL
Maxmimum content | 741 | 最大容量 |
Number of Bays | 29 | 货格数 |
Width of Bays | 3.15 | 货格宽度 |
Number of Levels | 13 | 货架层数 |
Place in Bay | 2 | 货格载货数 |
(2) 执行类参数的设定 ①堆垛机 (ASRSvehicle) 参数的设定如表5所示;②叉车 (Transporter) 参数的设定如表6所示。
表5 堆垛机参数 导出到EXCEL
Load time | 3 | 货叉装货时间 |
Unload time | 3 | 货叉卸货时间 |
Lift speed | 4 | 起升速度 |
Maximum Speed | 15 | 水平行走速度 |
Acceleration | 0.5 | 加速度 |
Deceleration | 0.5 | 减速度 |
表6 叉车参数 导出到EXCEL
Load time | 2 | 叉车装货时间 |
Unload time | 2 | 叉车卸货时间 |
Lift speed | 1 | 货叉起升速度 |
Maximun Speed | 24 | 水平行走速度 |
Acceleration | 1 | 加速度 |
Deceleration | 1 | 减速度 |
2.3 分拣系统的仿真建模
分拣系统是整个仓储系统的关键环节, 它依据顾客订货要求或配送中心送货计划, 迅速、准确地将商品从货架储位运送到分拣出口, 并按照一定方式进行分类、集中, 拣选后的托盘通过输送系统返回到立体仓库的货架区储存, 等待下一次分拣作业过程。分拣系统要求:
(1) 每个分拣出口都可以接收下游不同货架实体所存放的待分拣商品;
(2) 分拣后的托盘按最短路径策略查找最近的入库口, 由输送系统运送托盘回原货架;
(3) 待分拣的托盘进入分拣处理器, 由操作人员按订单拣选出库, 对于简化模型的分拣系统, 操作人员每次拣选2箱货品出库。
分拣是仓储系统作业中最繁锁、工作量最大的环节, 也是仓储作业系统的核心。分拣作业的速度和质量直接关系到整个仓储系统的服务水平, 合理利用机械、自动化设备, 采用新技术以节约作业时间、降低分拣错误率, 是构建分拣系统的目标与关键。分拣系统仿真模型控制流程如图4所示。
3 仿真模型运行及结果分析
根据系统实际作业周转量定义仿真时间, 运行模型进行仿真计算, 可模拟各台设备的运行, 得出计算结果, 从而检验设备的性能参数设计是否合理, 物料工艺流程是否简洁流畅, 物料流量是否能满足生产要求, 并最终结合实际确定设计方案。本文重点研究讨论该仓储系统的2个核心子AS/RS系统和分拣系统的运行结果。
在正常出入库状态下运行仿真模型, 设定仿真时间为8 h (28 800 s) , 考虑到系统开始运行时段, 仿真系统初始化运行1 h (3 600 s) , 根据实际情况, 该仓储系统的仿真为终止型仿真, 设置模型一次仿真运行时间为9 h (32 400 s) 。
考察平均入库量为37盘/h, 在入库量为30 000箱货品的情况下, 通过Flexsim Chart工具查看仿真结果, 系统堆垛机利用率如表7所示。
针对AS/RS第1跨区输送系统的阻塞率 (图略) 进行了研究:在8 h出入库状态下, 该输送系统的阻塞率最高达0.065%, 大多控制在0%左右, 阻塞率低, 设备布局合理。但堆垛机设备利用率较低, 存在设备闲置的情况, 这主要与订单出入库策略设置和堆垛机的数量有关。在今后的研究工作中将重点研究实际仓储系统的出入库策略, 增加物流设备的利用率, 更真实有效地仿真实际仓储系统的运行需求。
表7 堆垛机利用率 导出到EXCEL
堆垛机 1 |
堆垛机 2 |
堆垛机 3 |
堆垛机 4 |
堆垛机 5 |
堆垛机 6 |
堆垛机 7 |
堆垛机 8 |
堆垛机 9 |
堆垛机 10 |
堆垛机 11 |
堆垛机 12 |
堆垛机 13 |
堆垛机 14 |
堆垛机 15 |
|
利用率 | 22.47% | 6.13% | 20.13% | 25.68% | 10.63% | 15.35% | 25.57% | 20.68% | 18.59% | 21.47% | 21.57% | 21.52% | 21.86% | 22.56% | 40.17% |
仓储系统的仿真控制技术路线如图5所示。
4 结论
进行了基于Flexsim开发平台的物流仓储系统的建模与仿真研究, 将系统建模和仿真技术充分应用到物流仓储系统的规划和运作分析中, 针对AS/RS系统和分拣系统, 探讨了系统建模和作业控制流程仿真分析方法, 并对仓储系统进行了优化分析, 对系统改进提供了决策依据, 这对现有仓储系统的优化具有一定的指导作用。